Capstone Green Energy Revolutionizes Product Documentation & Business Partner Support with Documoto
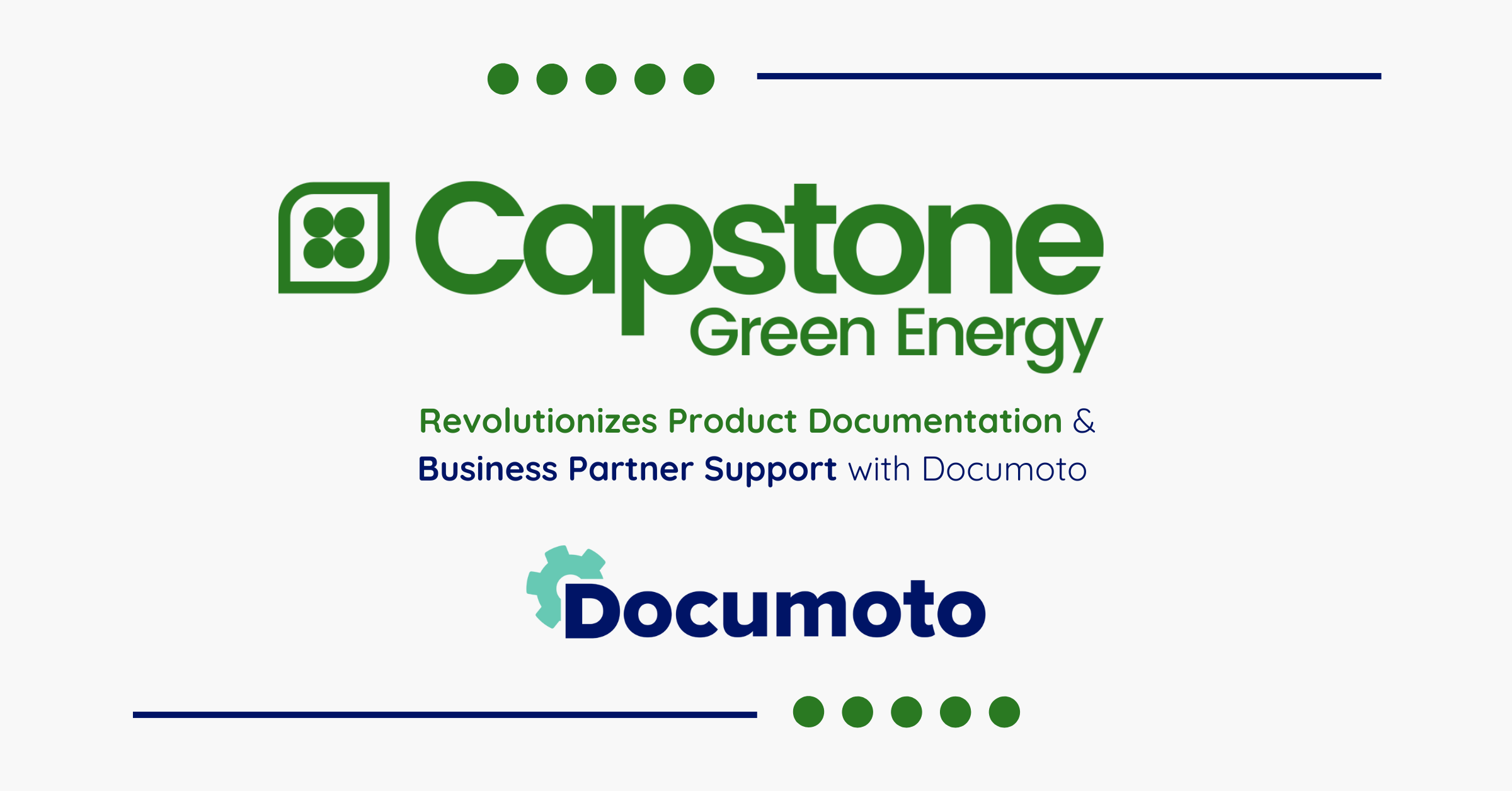
MARCH 2025 – USA
Overview
Capstone Green Energy is a global leader in innovative, low-emission energy solutions. Their advanced microturbine technology enables businesses to generate reliable, efficient power on-site, reducing reliance on the grid and minimizing energy costs. Their microturbines capture waste heat to support Combined Heat and Power (CHP) and trigeneration (CCHP) applications, maximizing efficiency and sustainability. Designed for versatility, Capstone microturbines run on a variety of fuel sources, including clean-burning natural gas and renewable biogas. With patented air bearing technology that eliminates the need for oil or coolants, the systems require minimal maintenance, providing a cost-effective and environmentally responsible energy solution for a wide range of industries.
To streamline operations across marketing, distribution, production, and aftermarket, Capstone Green Energy utilizes Documoto as a Complete Content Ecosystem. By importing all documentation, product and parts into Documoto, they enable tagging, indexing, categorization, and advanced search capabilities. This transition has greatly improved operational efficiency and effectiveness for both business partners and employees.
The Need for Change
Before adopting Documoto, Capstone Green Energy managed product documentation through SharePoint and relied on PDF Aftermarket Parts Books, which presented several challenges:
- Complicated Navigation: While functional, the SharePoint system was not user-friendly. Navigating the documentation structure required a deep understanding, making it frustrating for new or infrequent users. Additionally, setting permissions to control content visibility was challenging since this feature was not available, preventing end users from having access.
“Users would log in and have to find the right [thing]… go through folders and look for things, without the capability to search for keywords within documents, as that was simply how SharePoint was structured.” - Grant Terzer, Senior Director of Product Management
- Redundant Documentation: The inability to relate files forced the team to store duplicate documents across multiple locations. Grant explained, “We had to put documents in duplicate places because there was no way to relate it to one another,” which also created challenges for revision control.
- Aftermarket Parts Management: Part information was provided in PDF books with parts listed in table format. This system lacked visualization of where parts were used and did not connect to relevant service documentation (e.g., Service Notices, Service Bulletins, Work Instructions, Retrofit kits). Users had to manually search through a catalog of over 5,000 parts, relying heavily on expertise to identify the correct items. Many requests were sent via email with attached pictures, requiring Capstone’s Customer Service representatives—and often Engineering—to verify part numbers.
- Aftermarket Parts Ordering: Capstone’s parts identification process previously relied on customers either emailing pictures to customer service or navigating a PDF aftermarket parts book. Once a part was identified, business partners had to place orders through a separate CRM, requiring Capstone to manage pricing across multiple systems—making updates cumbersome. As a result, pricing revisions were typically conducted once a year through a bulk update to the price book. This process further complicated part orders, often leading customers to attempt to purchase superseded or obsolete parts, which increased the time and effort needed to process orders.
- Product Catalogs: Creating product catalogs was once a lengthy process, often taking weeks due to the need for reformatting and reorganizing documents. Updates were typically made annually, which frequently delayed the delivery of the latest product information to our business partners.
- Scheduled Maintenance: Scheduled Maintenance documents provided only high-level intervals with generic part names, lacking specific part numbers due to the variety of product configurations. Work Instructions were referenced but became time-consuming to update as engineering changes and parts obsolescence required frequent revisions.
Transition to Documoto
Initially, Capstone focused on supporting its business partner network by providing product support documentation, interactive product books for all offerings, and a limited release of exploded-view aftermarket parts books. However, as the team gained a deeper understanding of Documoto’s capabilities, they began discovering new opportunities to enhance various aspects of the organization while improving the overall user experience.
This shift expanded the possibilities of what Capstone could achieve with Documoto. Its user-friendly interface and intuitive design made managing product documentation and aftermarket parts significantly more efficient.
“Documoto is so much easier to use than SharePoint. As our expertise with Documoto continues to grow, we continue to identify new and valuable ways to streamline operations and elevate the user experience across all aspects of our organization.” - Grant Terzer, Senior Director of Product Management
Enhanced Accessibility and Search-ability
Documoto's capabilities have drastically improved how users find Marketing, Sales and Aftermarket information. Grant emphasizes this transformation:
“It became much easier for people to find the information they needed because we could now link the correct documentation to our product lines and associate the appropriate service materials with specific parts. The powerful search capabilities enabled keyword searches across all media, including brochures, manuals, drawings, schematics, troubleshooting guides, service documentation, and parts information—both at the document level and within the content itself. Previously, users had to navigate a complex Windows folder structure to locate a document and then search within it to find specific details.”
This functionality caters to different user preferences by offering both traditional and modern navigation styles, allowing users to choose between visual Browse Flows and keyword-driven Search Results.
“The ability to navigate using a visual browse flow—by selecting tiles in a way that feels similar to the Windows structure—while also having the option to search for information using keywords enables us to accommodate various user preferences and search habits.”
One Platform for Our Business and Partners
With Documoto, all of Capstone's documentation is now centralized:
- Members Only: The ability to set different access levels for each user has allowed Capstone to incorporate information from multiple internal departments while providing our business partners and their end users with secure access to Capstone’s new Document Library.
- Product Catalogs: All product offerings can now be easily visualized with images, descriptions, and pricing. Relevant sales and technical documentation were related for quick access, and the product catalog can be effortlessly exported to a PDF format. Updating the catalog now takes just a few hours, significantly improving efficiency and accuracy.
- Parts Catalogs: Parts can now be visualized through exploded view diagrams, enabling users to quickly identify their placement and verify compatibility with their equipment. Essential information, including work instructions, service notices, and bulletins, are related for easy reference. Additionally, related parts can be cross-referenced as alternatives or marked as “required” for ordering alongside a specific part.
- Shopping Cart Functionality: The Shopping Cart allows users with designated access to add products and/or parts to the Shopping Cart, which can be saved, downloaded as a CSV, or emailed. For technicians, this feature is especially valuable in the field, enabling them to add parts to the Shopping Cart while troubleshooting. This effectively allows the technician to generate an accurate parts list for incorporation into a field service report and parts order. For sales personnel, it streamlines project planning by allowing them to select the required equipment, add it to the Shopping Cart, save it as needed, and quickly calculate total equipment costs for budgeting or proposals.
- Request for Quote (RFQ) and Purchase Orders: Once the required parts have been added to the Shopping Cart, authorized users can use the Cart to place purchase orders or request formal quotes and lead times directly through Documoto. Parts managers and procurement teams can now easily order parts within minutes without needing to be part experts.
- Scheduled Maintenance Books: Capstone has innovatively leveraged interactive parts books to develop model- and fuel-specific scheduled maintenance guides for microturbines. These guides feature service interval pages with detailed illustrations of part locations, required maintenance actions, and corresponding part numbers. This approach has greatly improved service technicians' ability to prepare for maintenance visits, ensuring they have the correct parts on hand. Additionally, it streamlines the ordering process for parts managers and procurement teams, enabling them to accurately order necessary parts in advance, reducing errors, and ensuring the reliability of operating equipment.
- Marketing Resources: The addition of marketing resources gives business partners quick and convenient access to a comprehensive collection of up-to-date materials to support their efforts. This includes logos, images, and branding guidelines, as well as product brochures and datasheets. The library also features written and video case studies, marketing support forms (utilizing microsites or embedded HTML-based zipped mini-sites), presentation decks, corporate videos, and a giveaway catalog with online ordering capabilities. High-quality marketing collateral, such as brochures and product images, are readily available to business partners. Capstone’s integration of various file formats in Documoto ensures these resources are both easily accessible and simple to navigate, empowering business partners to more clearly communicate with potential customers and to close deals more efficiently.
- Training Materials: Easy access to training resources, including product familiarization, microturbine technical training, and technician refresher courses, allows Capstone to simplify the onboarding process for new employees and business partners. Users can browse the training catalog to explore available course offerings and navigate the live training calendar, while business partners can easily place orders for required courses. Microsites play a key role in hosting training courses and integrating the training calendar seamlessly. Learn more about how Microsites are being utilized in an upcoming Customer Showcase feature.
- Manuals: Comprehensive guides for all products and systems, including user manuals, product specifications, technical references, application guides, installation instructions and service notices/bulletins and forms that utilize the Microsoft file types that are viewable in Documoto without downloading.
- CAD File Accessibility: Capstone offers CAD model files through Documoto, giving business partners seamless access to download and integrate them into their systems. This enhances accuracy in modeling and installation planning, allowing business partners to visualize how Capstone products will integrate within a customer’s infrastructure.
- News Items: Provides a mechanism for Capstone to communicate across all aspects of the business, whether for internal communications, important updates on new product offerings, or service notifications. The system also includes the ability to add “Must Read” notifications as needed, ensuring critical information reaches the right audience.
- Documoto for the Production Floor: Capstone is also working to integrate Documoto into the production floor, providing all manufacturing personnel with easy access to the most up-to-date documentation, work instructions, and assembly information. This integration will centralize all manufacturing instructions and procedures, enhancing both efficiency and accuracy.
With Capstone’s ecosystem now established, the company is exploring new workflows to streamline operations and eliminate inefficiencies within its sales and service teams. Grant noted, “Documoto has opened up new possibilities and new ways to do things.”
Conclusion
Capstone Green Energy’s adoption of Documoto has not only streamlined documentation management but has also cultivated a culture of efficiency and accessibility. The platform serves as a crucial resource for business partners and internal teams, enabling them to quickly locate information and accurately identify necessary parts and documents.
As Capstone continues to expand, Documoto remains a cornerstone of its operations, strengthening business partner support and fostering seamless collaboration across all departments.
The ability to identify the correct part within minutes using the intuitive layout and powerful search engine, combined with interactive scheduled maintenance books and shopping cart functionality, has driven an increase in revenue orders. Enhanced part visibility and compatibility have encouraged many business partners to proactively stock spare parts, improving the overall customer experience. With everything now integrated into a single system, efficiency and convenience have reached new levels.
Contact Information
Capstone Green Energy: https://www.capstonegreenenergy.com/
Grant Terzer
- Role: Senior Director of Product Management
- Responsibilities: Grant oversees order management, technical publications, technical training, product management, applications engineering and controls commissioning at Capstone. He leads a team dedicated to improving the accessibility of product information for both business partners and internal teams.
Rene Flores
- Role: Senior Product Specialist
- Responsibilities: Specialist in matters related to microturbine configurations and customizations, engine fuel use, and combustion emissions. Provides cross-departmental and specialized field support. Creates highly specialized, customer-facing documentation. Administrator and publisher for Capstone’s Document Library.
Paul Breault
- Role: Product Design Engineer
- Responsibilities: Create technical illustrations for all customer-facing documentation using a variety of software tools. This includes generating detailed part and assembly drawings, electrical schematics, mechanical diagrams, and photorealistic renderings of parts and assemblies.
Key Contributions:
Grant, Rene and Paul have been instrumental in shifting from traditional document management systems like SharePoint to Documoto for managing product and part information. They emphasize the need for a user-friendly content ecosystem that improves organization, searchability, and accessibility of all product documentation.